- Overview
- FAQ
Basic Info.
Model NO.
Ring die
Processing Technics
Mixing-before-Crushing
Screen Mesh
With Screen Mesh
Grinding Equipment Type
Roll Crusher
Pellet Mill Type
Ring Die Pelleter
Bulking Machine Type
Twin Screw Bulking Machine
Expanding Method
Dry Expansion
Condition
New
Applicable Materials Shape
Powder
Warranty
12months After Delivery
Brands
C.P.M/Buhl.Er/Muyang Pellet Machines
Weight
80-300kg
Application
Wood/ Feed Pelleting Industry
Heat Treatment
Vacuum Type
Ratio
4.5-16
Hole Size
2-12mm
Material
X46cr13
Transport Package
Wooden Case
Specification
5.0X60/55
Trademark
Gamma Tech
Origin
Jiangsu, China
HS Code
843699000
Production Capacity
300 Sets Per Month
Packaging & Delivery
Package Size
50.00cm * 50.00cm * 50.00cm
Package Gross Weight
120.000kg
Product Description
X46CR13 VACCUM HEAT TREATMENT FEED MACHINE WOOD PELLET MILL RING ROLLER DIE AS SPARE FORGING PARTS OF PELLET MACHINE
1.Biomass pellet machine: wood pellet mill, sawdust pellet mill, grass pellet mill, straw pellet mill, crop stalk pellet machine, alfalfa pellet mill etc.
2.Fertilizer pellet machine, all kinds of animal/poultry/livestock feed pellet machine.
We can make many famous models ring die & roller shells,such as:
SZLH,CPM, B.uhler, PTN, Andritz Sprout, Matador, Amandus Kahl, Muyang, Paladin, Sogem, Van Arssen, Yemmak, Promill,etc.
We make all kinds of pellet mill ring dies according to customers' drawing.
• For Zhengchang pellet mill: SZLH250, SZLH300,SZLH320,SZLH350,SZLH400,SZLH420,SZLH508, SZLH678, SZLH768, etc
• For Muyang pellet mill: MUZL180, MUZL350, MUZL420, MUZL600, MUZL1200, MUZL610, MUZL1210, MUZL1610, MUZL2010;MUZL350X, MUZL420X, MUZL600X, MUZL1200X(Especially for shrimp feed pellet, diameter: 1.2-2.5mm)
• For Awalia pellet mill: Awalia 420, Awalia350, etc
• For B.uhler pellet mill: B.uhler304, B.uhler420, B.uhler520, B.uhler660, B.uhler900, etc.
• Other kinds.
Product Name | alloy steel forging ring die for pellet maker machine |
Material | alloy steel |
Color | nickel white |
Standard | Meet the Industry standard |
Grade | First level |
Brade | Rock |
Thread | coarse, fine |
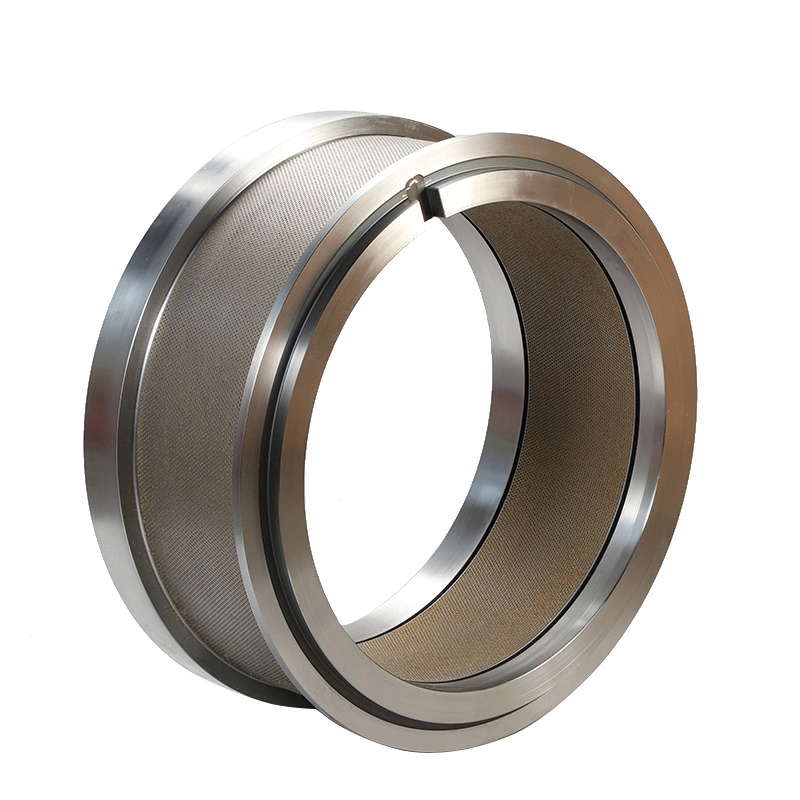
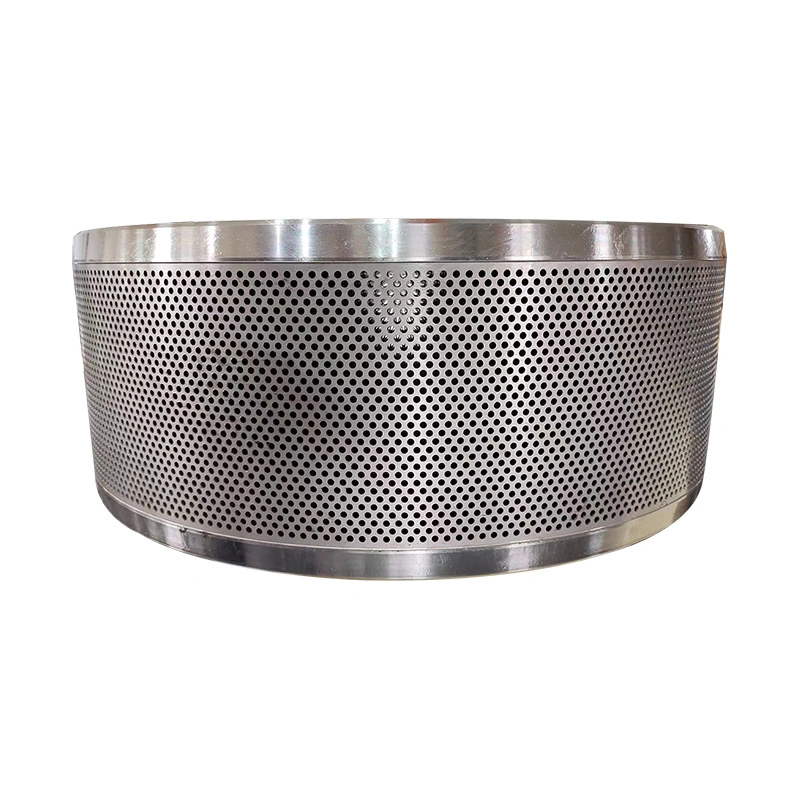
Manufacturer Process and Facility:
Process for making ring dies / flat dies spare parts, pellet dies
Blank raw material Forging---Rough turning---Half finished turning---Drilling the hole---Grinding inner bore---Treaded hole--- Keyway milling---Heat treatment---Finish turning---Package
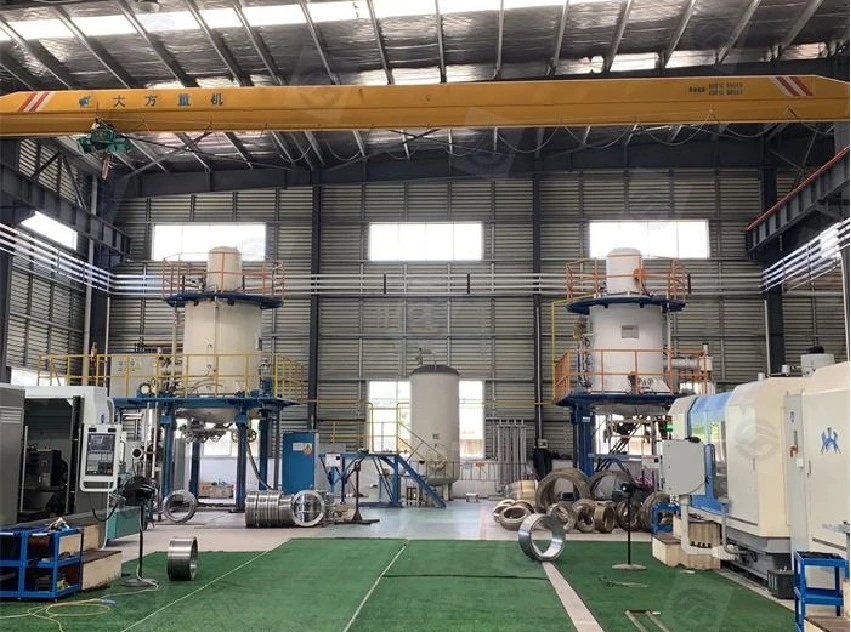
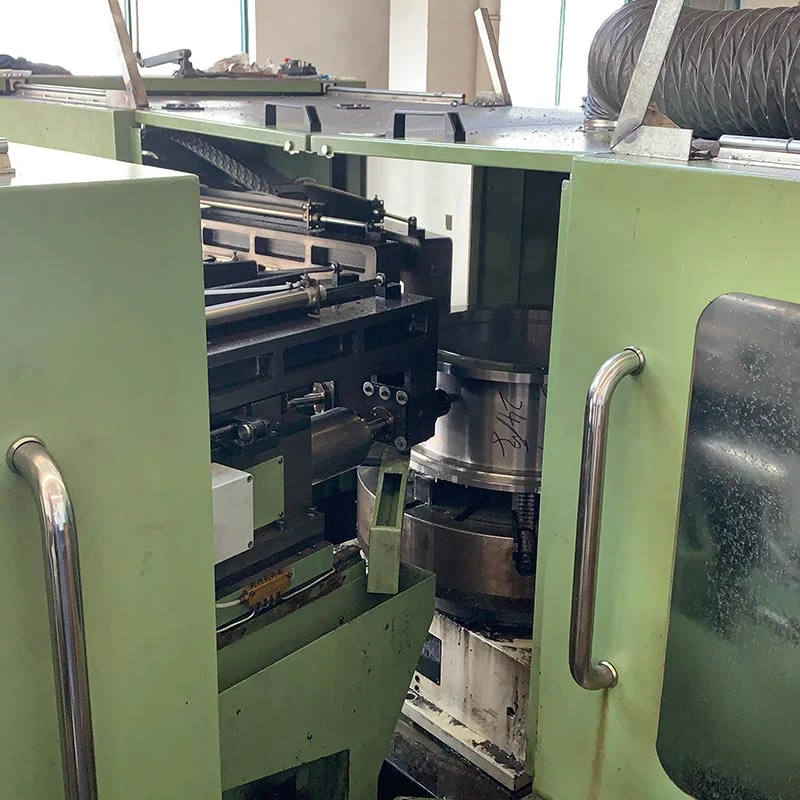
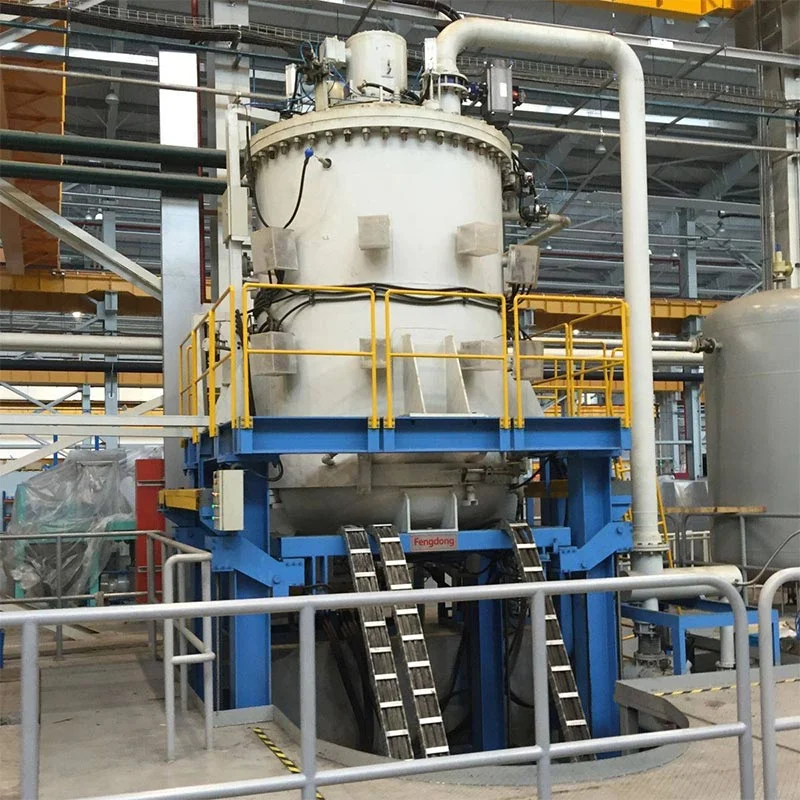
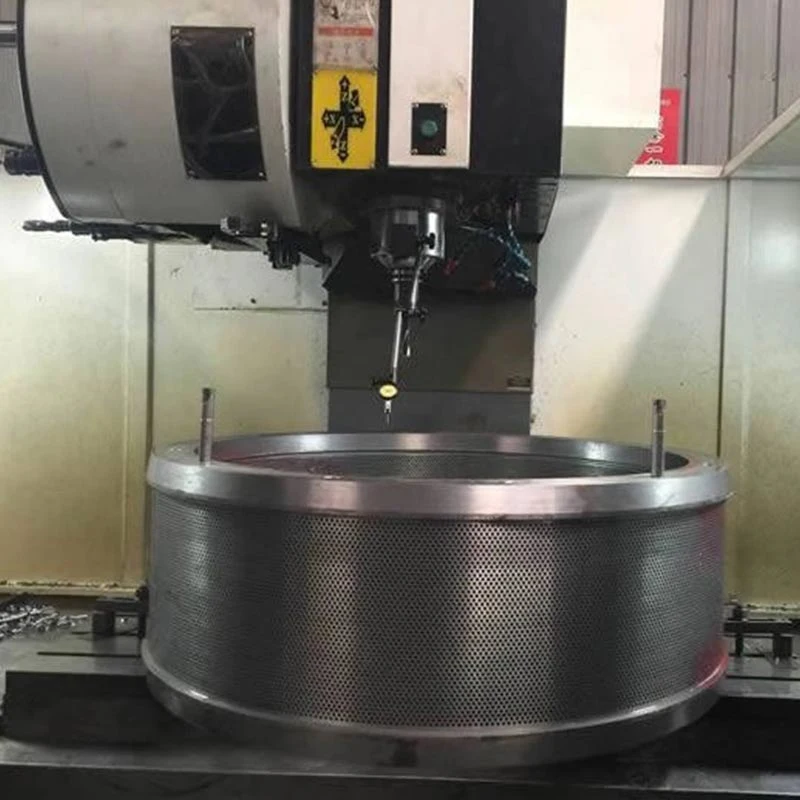
FROM FACTORY TO CLIENTS , REDUCE SPARE PARTS COST FOR ALL FEED MILLS IN THE WORLD .
Q1. How can the die characteristics be determined?
A: This is where experience becomes an important factor. The selection of a die specification is often the result of a compromise between the different needs of the many formulas produced in a production plant and from the specific properties of the actual plant. The most common mistake is to assume that the die is the cause of all problems. Pellet quality can depend on many factors that have nothing to do with the die, the most common being poor steam-conditioning of the formulas. To overcome these problems, dies with a high compression index (i.e. large thickness) are used.Q2. What is your terms of payment?
A: T/T 30% as deposit, and 70% before delivery. Below 1000USD order, 100% should be paid as deposit. We'll show you the photos of the products and packages before you pay the balance.
Q3. What is your terms of delivery?
A: EXW, FOB, CFR, CIF.
Q4. How about your delivery time?
A: Generally, it will take 30 to 60 days after receiving your advance payment. If we have your popular model as our storage, we can deliver within 2 days. The specific delivery time depends on the items and the quantity of your order.
Q5. Can you produce according to the drawings?
A: Yes, we can produce by your technical drawings or your samples.
Q6. Do you test all your goods before delivery?
A: Yes, we have 100% test before delivery
Q7. How do you make our business long-term and good relationship?
A:The experience we have gained over the years ensures:
•high-quality raw materials including high chrome steels
•state of the art plant and machinery implementing cutting edge technology
•gun drilling and mirror-polishing of holes
•vacuum hardening - heat treatment
•negligible die distortion during heat treatment
•rigorous quality control prior to delivery