Basic Info.
Packaging & Delivery
To be negotiated ( > 1 Pieces)
Product Description

The majority there are 2-series milling machines, Wet Grinders & Cell Mill
The wet grinder is a new type of vertical grinder that integrates and combines technologies of both gravity and fluidization. To through the rotational energy of the stirring wheel to drive the medium ball and slurry to generate turbulence then interactional colliding, shearing, and squeezing to get the best fineness of 300-nanometer particles of powder.
Low investment, cost-effective operation, stable process, space-saving, and easier installation are the advantages of the wet grinder.
The capacity of the machine is flexible to customize from 1 kg to 100 tons per hour.
Cell mill is a mechanical airflow mill, designed for the production of ultra-fine mineral powder which requests an extremely high standard of particle size. It conducts the practical process of drying after depolymerization, then synchronously implements shaping, and surface coating for powders.
The moisture content could be controlled at 0.01% while achieving 99.2% of coating and 99.8% of activation.
The capacity of the machine is flexible to customize from 50 kg to 15 tons per hour. The maximum evaporation of water is 3 tons per hour.
Features of Wet Grinder:
- Thanks to the excellent grinding chamber structure design, the medium ball generates greater pressure, restricting and forcing the material to contact the grinding medium in an optimal manner.
- The energy distribution of the grinding is constant for any given height and radius.
- The rotation of the grinding tray drives the micro-beads medium ball to produce more grinding and shearing points, and one ball is equivalent to a small crusher.
- Compared to the ball mill gets its energy by rotating the cylinder, the main shaft drives the grinding tray is the key reason to reduce the energy consumption of wet grinding.
- The wet mill is vertically arranged, with feeding at the bottom and discharging at the top, so as to save the pressure of the slurry sealing device and reduce the feed inlet, and the equipment operation and maintenance are easy.
- The efficiency and fineness of wet grinding are always superior to other mills. The fineness of wet grinding varies with the difference in ore characteristics, but the particle size can be controlled within 0.1-0.5 microns in general.
- Cell mill is based on a modular design, which allows optimum design for each piece of equipment for different environments while maintaining the basic principles and the same parts.
- The equipment performance is optimized by varying the number of layers of the rotor and the number of blades. The separator installed in one piece will not affect the structure of the main grinding chamber.
- The structural design of the module makes it easy to maintain and replace consumable parts.
- The material of the rotor blade can be hardened steel, stainless steel, or steel-bonded tungsten.
- The material of the grinding groove shall be steel, stainless steel, or high-alumina ceramic.

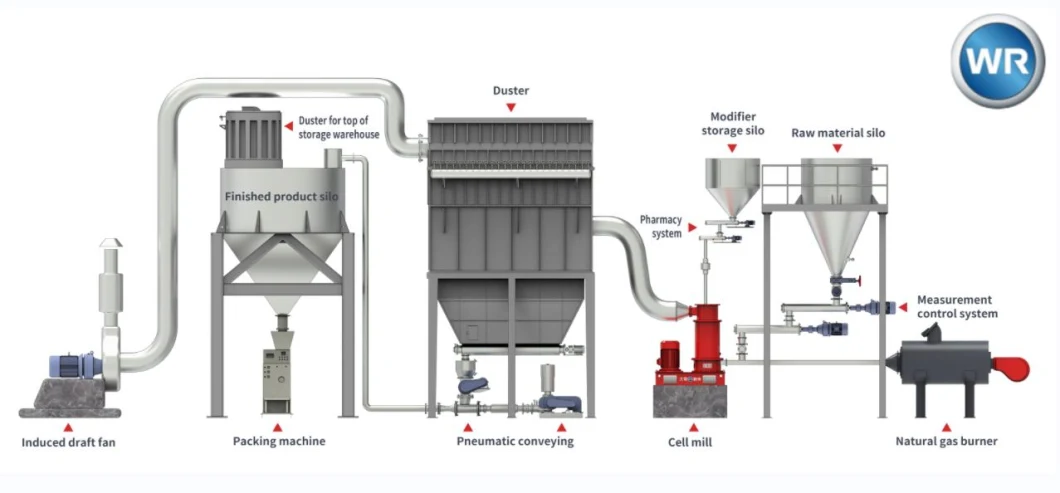
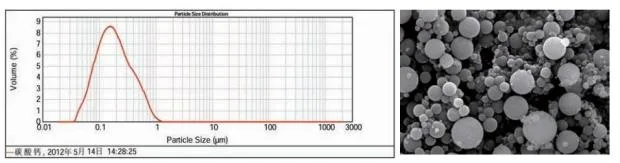
Model | Wet Grinder (ultrafine grinding, fineness of nanometer is achievable) | |||||||
WRMJ100 | WRMJ150 | WRMJ200 | WRMJ500 | WRMJ1500 | WRMJ4000 | WRMJ6000 | DZM3500 | |
Power | 10-55KW | 10-55KW | 10-55KW | 75KW | 160KW | 250KW | 355KW | 1180kw |
Slurry Output Ton/H | 0.02-0.1 | 0.05-0.2 | 0.06-0.2 | 1.0-1.5 | 1.8-3.0 | 2.6-5.8 | 4.5-9.5 | 55.5-100 |
2 μM Fineness | D60-D98 | D60-D98 | D60-D98 | D60-D98 | D60-D98 | D60-D98 | D60-D98 | D60-D90 |
Max Feeding Size | ≤1mm | ≤1mm | ≤1mm | ≤1mm | ≤1mm | ≤1mm | ≤1mm | ≤1mm |
Output Size | 0.1-45um | 0.1-45um | 0.1-45um | 0.1-45um | 0.1-45um | 0.1-45um | 0.1-45um | 0.1-45um |
Solid Content% | 50%-70% | 50%-70% | 50%-70% | 50%-70% | 50%-70% | 50%-70% | 50%-70% | 50%-70% |
Power Consumption KW/T/H | 35-225 | 38-154 | 38-155 | 35-105 | 37-124 | 30-134 | 26-165 | 12-26 |
Medium Ball Consumption (Kg/Ton) | 0.2-1.6 | 0.2-1.6 | 0.2-1.6 | 0.2-1.6 | 0.2-1.6 | 0.2-1.6 | 0.2-1.6 | 0.2-1.6 |
Dispersant Consumption (Kg/Ton) | 3-8 | 3-8 | 3-8 | 3-8 | 3-8 | 3-8 | 3-8 | 3-8 |
Wear/USD/T | 0.10 ~ 0.68 | 0.10 ~ 0.68 | 0.10 ~ 0.68 | 0.25 ~ 0.88 | 0.18 ~ 0.62 | 0.10 ~ 0.65 | 0.05 ~ 0.28 | 0.10 ~ 0.26 |
Motor Type | Motor Reducer Drive | Motor Reducer Drive | Motor Reducer Drive | Motor Reducer Drive | Motor Reducer Drive | Motor Reducer Drive | Motor Reducer Drive | Motor Reducer Drive |
Production Pattern | Continuous | Continuous | Continuous | Continuous | Continuous | Continuous | Continuous | Continuous |
Dimension (L*W*H, mm) | 1000*1000*1900 | 1100*1100*2000 | 1200*1200*2100 | 2500*1500*4500 | 3000*3000*5500 | 3600*3600*8600 | 4250*2500*3380 | φ3500*8100 |
Weight (Ton) | 1.3 | 1.5 | 1.7 | 4.5 | 9 | 13 | 17 | 80 |
Model | Cell Mill (Drying, Depolymerizing, Coating/Modifying, Spheroidizing) | ||||||
CM350 | CM500 | CM750 | CM1000 | CM1250 | CM1500 | CM2250 | |
Power | 22KW | 55KW | 90KW | 132KW | 160KW | 200KW | 280KW |
Capacity Ton/H | 0.1-0.3 | 0.8-1.2 | 0.8-1.5 | 2-2.5 | 2.5-3 | 3-3.5 | 4.0-5.5 |
Coating Rate | 99.2% | 99.2% | 99.2% | 99.2% | 99.2% | 99.2% | 99.2% |
Activation Rate | 99.8% | 99.8% | 99.8% | 99.8% | 99.8% | 99.8% | 99.8% |
Water Content% | 0.5‰ | 0.5‰ | 0.5‰ | 0.5‰ | 0.5‰ | 0.5‰ | 0.5‰ |
Max Feeding Size | ≤3mm | ≤3mm | ≤3mm | ≤3mm | ≤3mm | ≤3mm | ≤3mm |
Power Consumption KW/T/H | 70-100 | 45-68 | 60-112 | 52-66 | 53-64 | 66-57 | 56-70 |
Motor Type | Motor Drive | Motor Drive | Motor Drive | Motor Drive | Motor Drive | Motor Drive | Motor Drive |
Production Pattern | Continuous | Continuous | Continuous | Continuous | Continuous | Continuous | Continuous |
Dimension (L*W*H, mm) | 1730*1100*2168 | 1750*870*2017 | 2000*1100*2276 | 2648*1400*2455 | 2800*1600*2493 | 3400*1920*3627 | 5000*2500*4100 |
Weight (Ton) | 2.3 | 2.8 | 7.8 | 11 | 13 | 15 | 20 |

The main component is a vertically mounted multi-stage depolymerization wheel, each depolymerization wheel consisting of two supporting trays mounted on the spindle to clamp 200 blades. Depending on the specific load requirements, one cell mill can be fitted with 10 depolymerization wheel components, and up to 2000 depolymerization blades. The blades rotate at 110 m/sec and the 6mm of the grinding groove is a unique stiffening rib-type fixing strip. There are 160 turbulent "honeycombs" between the blade and the liner strip, the pressure, shear force, and friction force between them can quickly grind the material into superfine powder.
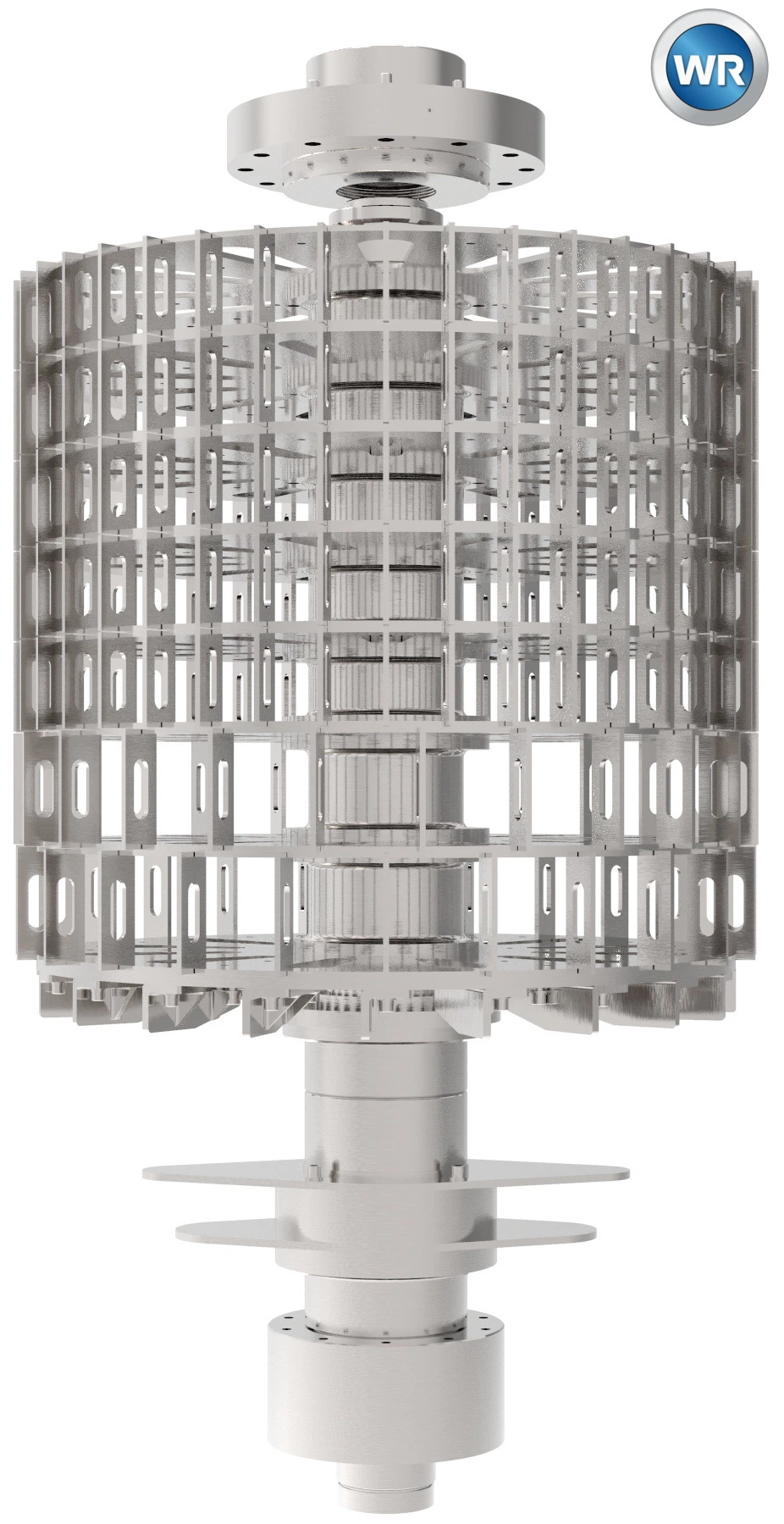
- Ultrafine Grinding, a professional solution provider of nanometer powder production.
- Sole Solution Provider with 70+ technical monopolies.
- Professional Solution Provider for production line/process from grinding to drying, depolymerizing, coating/modifying, and also spheroidizing.
- Cost-Efficiency: low energy consumption, low media consumption, low maintenance cost.
- Less Investment: lower requirement of foundation, space-saving, easy to install & maintain.
- No Pollution: no discharging of wastewater, exhaust emissions, and waste residue.
- Stable Process: smooth & quiet running/operating.
- Easy Operation: changing feed velocity to get different products.
- Customized Service to satisfy your each requierments.
- Lifetime After-Sales Service
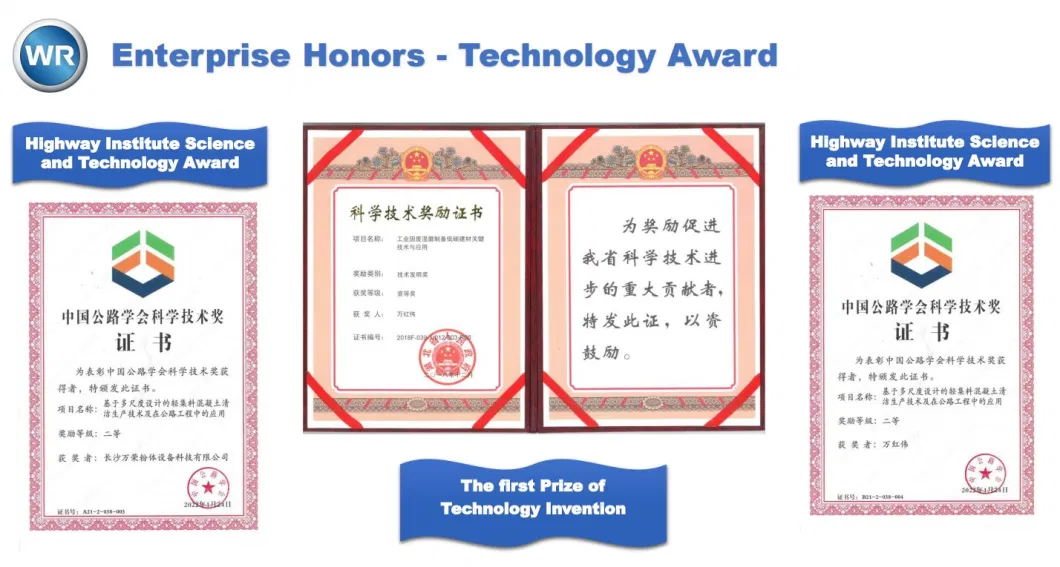

Changsha Wanrong Milling Equipment Technology Co., Ltd. was founded in 2008, as a high-tech enterprise of equipment manufacturers engaged in wet ultrafine grinding, drying, depolymerization, and mineral powder surface coating. Wanrong has rich experience and resources accumulated, with dozens of patents of inventions and a technical monopoly, Wanrong has won a very good reputation in the mineral powder business. Especially in terms of high productivity, low energy consumption, and excellent stability, Wanrong is highly praised and recommended by our customers.
Wanrong, the solution provider of nanometer powder production!
Customer Visit
Exhibitions
Team Activities
