Basic Info.
Product Description
Material | Hardness | Diameter | Outer diameter | Level | Certification |
X46Cr13/4Cr13(Stainless steel);20MnCr5/20CrMnTi(Alloy steel) or customized | HRC54-60 | 1.0mm-28mm | <1800mm | 1 | CE/ ISO |
Our ring dies are suitable for:
1. Biomass pellet machine: wood pellet machine, sawdust pellet machine, grass pellet machine, straw pellet machine, crop straw pellet machine, alfalfa pellet machine, etc.
2. Livestock and poultry/aquaculture feed pellet machine: pig/cattle/sheep/chicken/duck/fish/shrimp
3. Cat litter granulator
4. Compound fertilizer
Features:
1. Select high-quality refining and degassing blank outside the furnace
2. The mold adopts imported gun drilling and multi-station group drilling, the mold hole is formed at one time, the finish is high, the production feed appearance is beautiful, the output is high, the discharge is smooth, and the granules are well formed
3. The mold adopts the combined treatment process of the American vacuum furnace and the continuous quenching furnace, which is quenched uniformly, the surface finish is good, the hardness is high, and the service life is doubled.
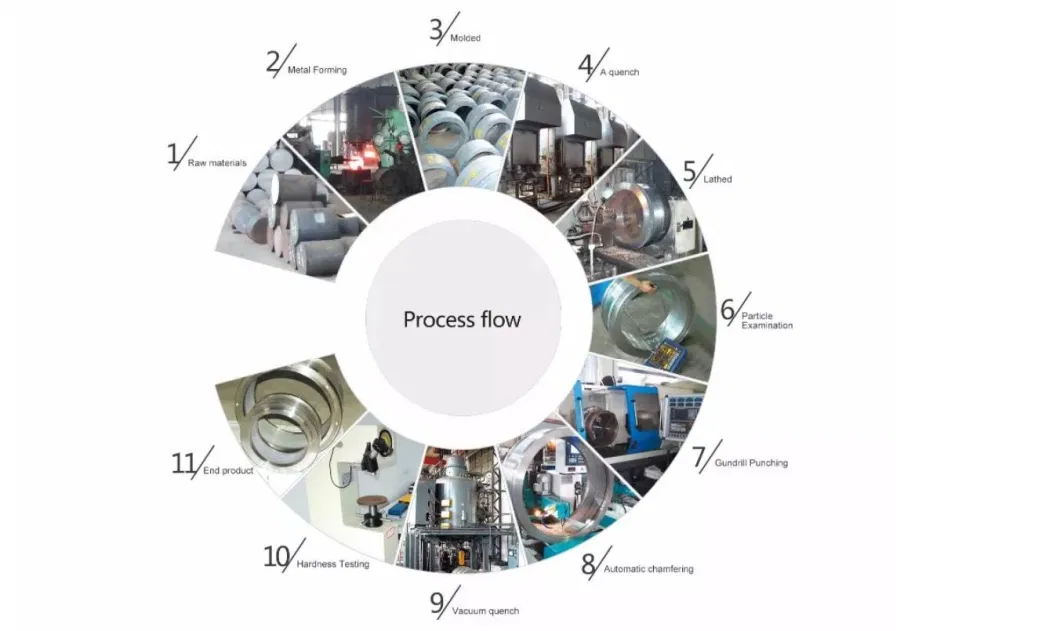
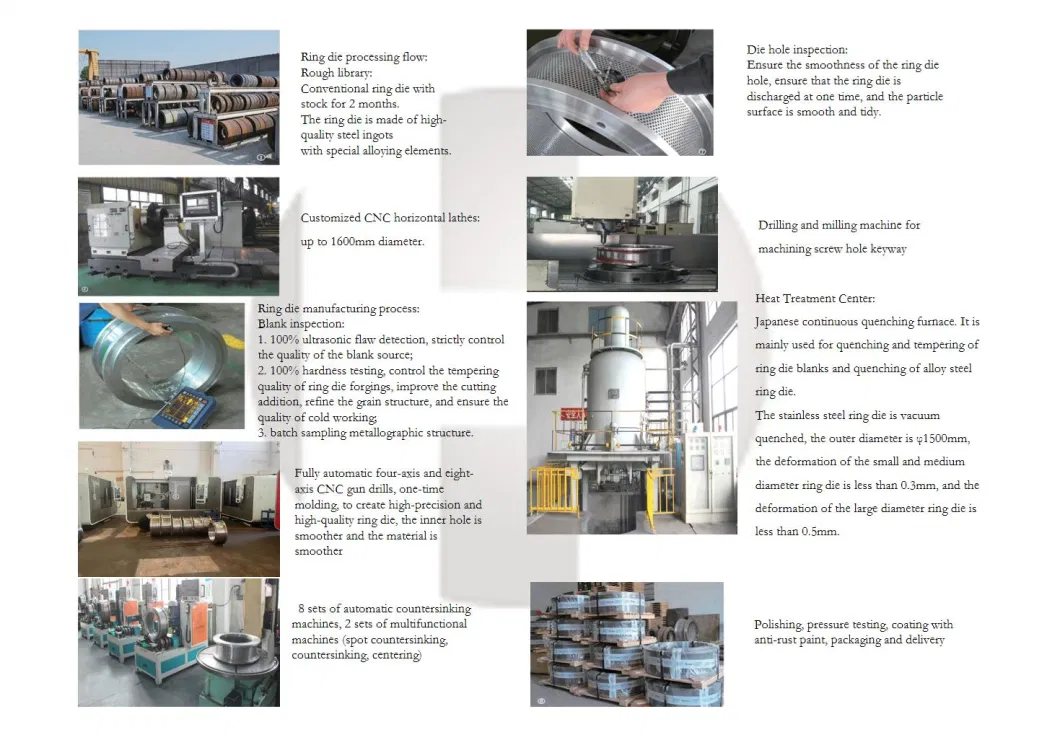
Correct Use and Maintenance of ring die
1. Ensure that the die hole is smooth, the material is evenly distributed on the working face (to improve the life of the ring die), and the feeding scraper (deflector) will guide the powder on the ring die cover into the rotating ring die. Change the angle of the feeding scraper to change the material distribution mode. The inner scraper (upper and lower) located on the inner side of the ring die transfers the material back to the working area. The excessive wear of the feeding scraper and the inner scraper will affect the production efficiency and the abnormal wear of the working surface of the ring die.
2. The granulator shall be operated under rated load and shall not be overloaded. High output requires correct ring die and correct raw material conditioning.
3. The initial particles will be very soft. Slowly increase the feeding amount until the particles become hard. This process should not be too urgent. The ring die must have a heating time. If the feeding is fast and dry, the die hole will be easily blocked.
4.The rolling, blocking, blind hole and pressing iron of the ring die shall be handled in time.
5.Avoid hard contact between the ring die and the press roll.
6.If the die hole is blocked, it is recommended to use oil for granulation and extrusion, or remove the ring die and soak it in oil before operation. If the above methods are not available, use a punch and an electric drill to drill out the filler, and be careful not to damage the die hole.
7.Hard steel tools shall not be used to hammer the ring die directly.
8. Reasonably assemble and use the magnetic absorption device to prevent metal objects from entering the granulation chamber and causing damage to the ring die. If iron is pressed into the die surface, it should be taken out in time.
9.Record the use of the ring die to fully understand the quality and life of the ring die.
10.In addition to the installation and operation manual, pay attention to the blanking opening of the capping granulator to prevent tools or other debris from falling into the cooler when replacing the new ring die.
11.Whenever the ring die is stopped, the die hole should be filled with non corrosive oily raw materials, otherwise the residual materials in the cold ring die hole will become hard, causing the die hole to be blocked or even corroded. Filling oil can not only prevent the hole from being blocked, but also wash away the residual fat and acidic materials in the hole wall.
12.The ring die and the press roll shall be used in pairs. The new die shall be matched with the new roll, or the old ring die and the old press roll shall be repaired before use to avoid abnormal wear caused by the use of the ring die press roll under abnormal coordination.
13. The damage of the ring die mostly depends on the wear of the working face. Regular visual observation should be made to correct the uneven wear of the ring die.
The environmental dies are classified according to their uses:
1.livestock and poultry (grain grains, forage grains)
2.aquatic products (fish, crab, shrimp)
3.fuels (sawdust grains, grass grains)
4.fertilizers (organic fertilizer, compound fertilizer, etc.).
According to the assembly form of the main engine, it is generally divided into two types: screw type and hoop type.
Fit of pressing roller and ring die.
Before the installation of the press roll, the sundries in the assembly hole shall be carefully cleaned and greased. The large side of the left roll shall face up to the right, and the large side of the right roll shall face down to the left. The press plate shall be installed in the hole.
1. The roller die clearance is adjusted by turning the eccentric shaft anticlockwise to make the clearance smaller and clockwise to make it larger. The new ring die shall be equipped with a new press roll with a clearance of about 0.2mm and a normal production time clearance of 0.3mm. The adjustment of the roll die gap is very important. The gap is too small, the roll die directly contacts, the wear is increased, and the horn hole edge is damaged by rolling; If the clearance is too large, the output will be affected, and the machine is easy to be blocked, or even cannot be granulated. The experience shared by the old master is that when the ring die is turned by hand, it is better for the pressure roller to turn passively.
2. The axial fit of the press roll and the ring die mainly means that the axial position of the press roll and the working face of the ring die should be correct. Most of the press roll working faces are 4mm wider than the working face of the ring die. The most ideal fit is to evenly distribute 2mm in the front and back. The measuring method is to measure the distance between the end face of the ring die and the end face of the press roll with a vernier caliper that can measure the depth, and then calculate whether it is reasonable before making adjustments. If changes occur, they usually occur after the replacement of the main shaft bearing, or non-standard pressure rolls and accessories are used.