Basic Info.
Model NO.
UFZ
Instruction
Video
Heavy Powder Application
Yes
Filters
Stainless Steel or Film
Suction Gun
Optional
Butterfly Valve
Yes
Solenoid Valve
Yes
Blow Back
Yes
Transport Package
Sea Worthy Packing
Specification
customized as per working situation
Trademark
UNITFINE
Origin
China
HS Code
8428320000
Production Capacity
300 Set Per Year
Product Description
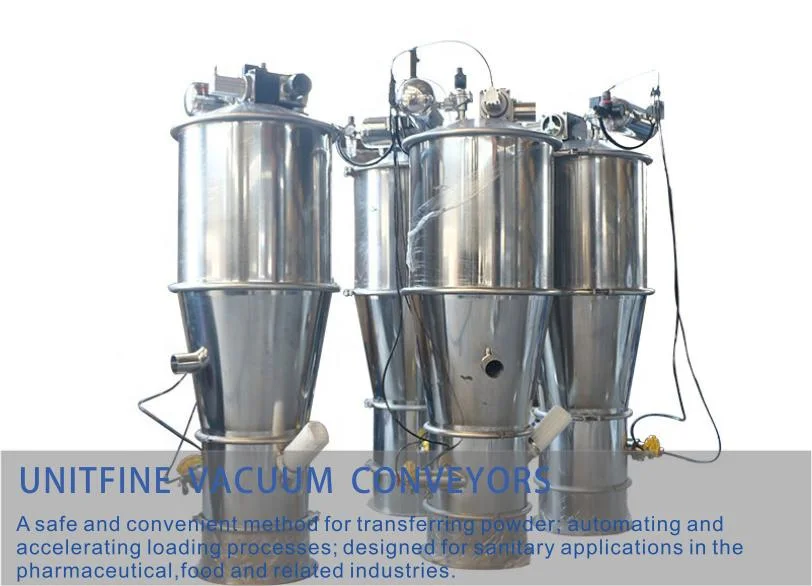
Introduction>>>
Vacuum Conveyor is the most advanced, perfect vacuum conveying equipment of powder material, granular material, powder- granular mixing machine, packing machine, injection molding machine, grinder etc, with the advantage of cost-reducing and no powder pollution.
The vacuum conveyor consists of a vacuum pump(no oil and water), stainless steel suction tube, flexible hose, PE filter or SUS 316 filter, compressed air cleaning device, pneumatic discharging device, vacuum hopper, and automatic level control device. This machine can reach the GMP standard and is the ideal feeding to the food industry and pharmaceutical industry.
Working Principle>>>
When the compressed air supply vacuum generators, vacuum generators produce negative pressure to form a vacuum airflow, the conveyed material arrives at the silo of the feeder through the feeder port. the filter in the hopper will separate completely the material and air. When the silo is filled with the materials, the PCB controller will automatically cut off the gas source, and vacuum generators stop working while the silo door automatically opens, then the materials fall into the hopper of the receiving device. Meanwhile, the compressed air will clean the filter automatically by pulse reverse valve. When the PCB controller reaches the settled time or the level inductor sends a signal of feeding materials. the vacuum feeder will repeat automatically this working process.
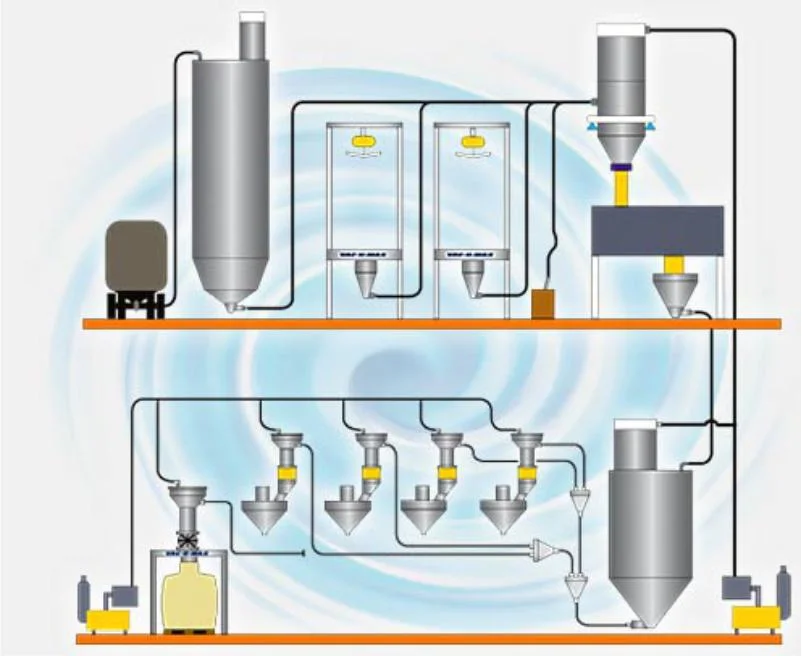
Application cases>>>
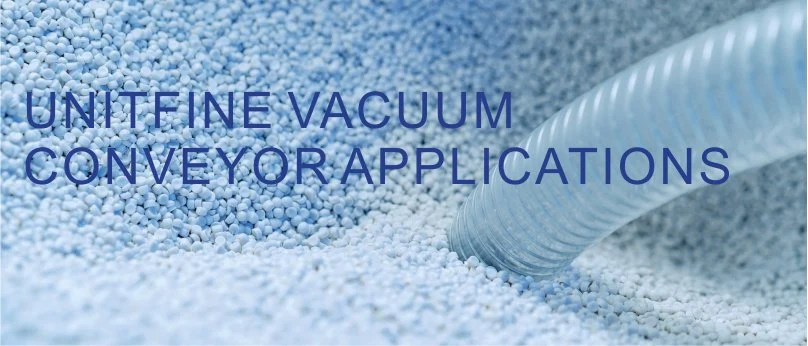
Food and Pharmaceutical Industries:
Powder and Granule Transfer: Vacuum conveyors are widely used for transporting powders, granules, and other bulk materials in the food and pharmaceutical industries. They are ideal for handling sensitive materials that require careful handling to prevent contamination.
Capsule and Tablet Conveying: In pharmaceutical manufacturing, vacuum conveyors are often employed to transport capsules and tablets between different processing stages, ensuring a clean and controlled environment.
Packaging: Vacuum conveyors are used for moving food and pharmaceutical products during the packaging process, helping to maintain hygiene standards and preventing product contamination.
Chemical Industry:
Chemical Powder Handling: Vacuum conveyors are suitable for the transport of various chemical powders and granules. They provide a dust-free and enclosed system, reducing the risk of exposure to harmful substances.
Electronics Manufacturing:
Component Handling: Vacuum conveyors are used to handle delicate electronic components during the manufacturing process. They can transport small parts without causing damage or contamination.
PCB Assembly: In the assembly of printed circuit boards (PCBs), vacuum conveyors are employed to move electronic components from one workstation to another without the risk of static discharge or damage.
Packaging and Material Handling:
Bag and Box Handling: Vacuum conveyors are used to handle bags, boxes, and other packaging materials on production lines. They can efficiently transport items without the need for manual handling.
Labeling and Coding: Vacuum conveyors are integrated into packaging lines for the efficient movement of products during labeling and coding processes.
Automotive Industry:
Part Transfer: Vacuum conveyors play a role in the automotive industry by transporting small parts between different stages of production. They are suitable for handling various materials used in automotive manufacturing.
Printing Industry:
Paper and Cardboard Handling: Vacuum conveyors are utilized in the printing industry for the movement of paper and cardboard sheets. They help in the automation of printing processes and reduce the risk of damage to printed materials.
Textile Industry:
Fiber and Yarn Handling: Vacuum conveyors are employed in the textile industry for the transportation of fibers and yarns between different stages of production, such as spinning, weaving, and finishing.
Woodworking Industry:
Wood Chip and Dust Extraction: In woodworking operations, vacuum conveyors can be used to transport wood chips and dust away from cutting and milling machines, contributing to a cleaner and safer working environment.
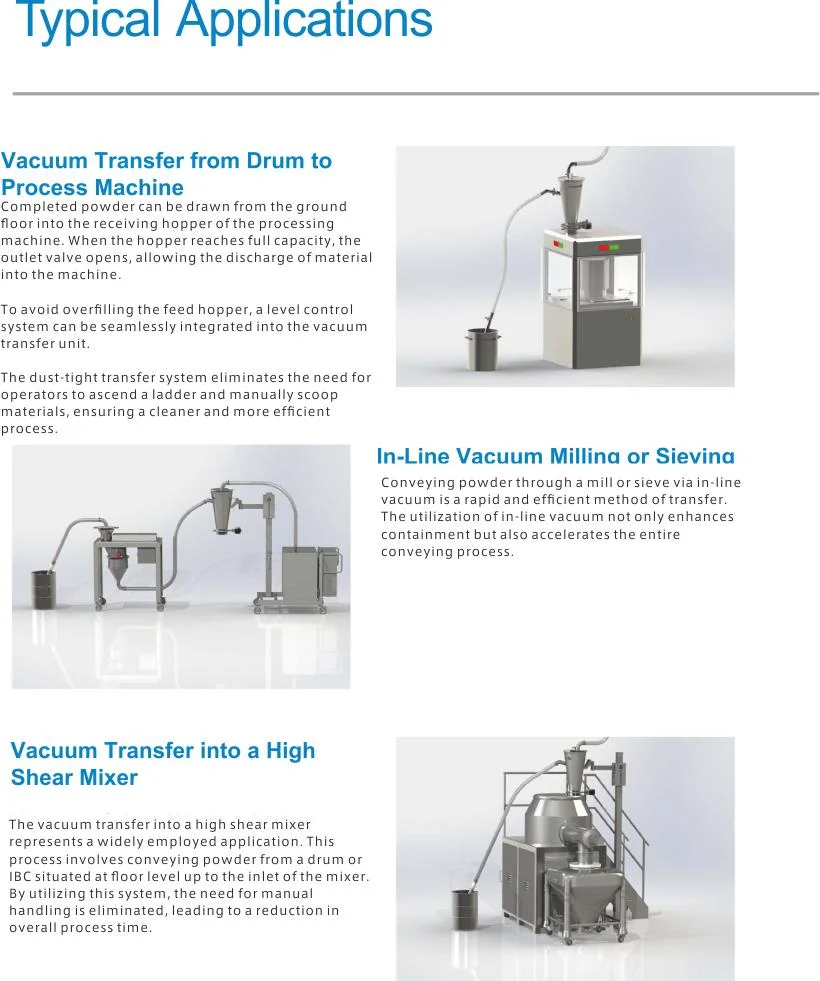
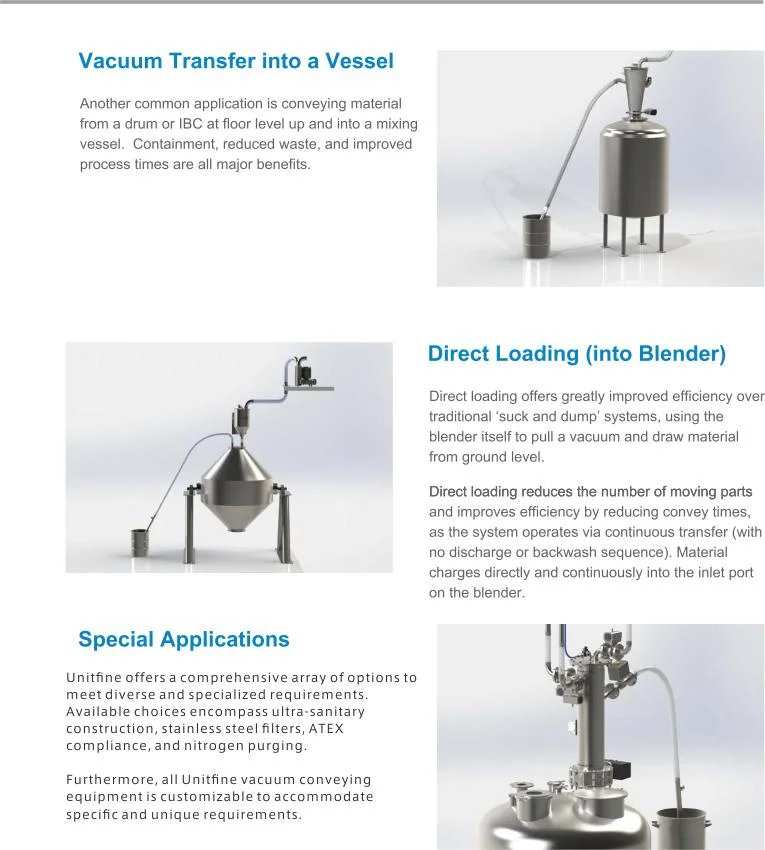
Models Available>>>
Model | UFZ180 | UFZ250 | UFZ320 | UFZ430 |
Equipment height | 850MM | 950MM | 1100MM | 1400MM |
Inner diameter | 180MM | 250MM | 320MM | 430MM |
Effective volume | 7L | 18L | 35L | 60L |
Equipment weight | 20KG | 35KG | 37KG | 55KG |
Blanking butterfly valve caliber | 150MM | 150MM | 320MM | 200MM |
Air consumption | (0L/min,0.6L/min) | (0L/min,0.6L/min) | (0L/min,0.6L/min) | (0L/min,0.6L/min) |
Vacuum flow | (0L/min,90L/min) | (0L/min,90L/min) | (0L/min,90L/min) | (0L/min,90L/min) |
Work pressure | (-92.5kpa,0kpa) | (-92.5kpa,0kpa) | (-92.5kpa,0kpa) | (-92.5kpa,0kpa) |
Throughput | (0.1t/h-0.5t/h) | (0.3t/h-0.8t/h) | (0.5t/h-2t/h) | (1.3t/h-5t/h) |
Applicable Item Properties | ||||
Applicable Material Type | Powder | Granule | ||
Applicable Material Temperature | (-10ºC-70ºC) | (-10ºC-70ºC) | ||
Applicable Material Humidity | (0%RH-20%RH) | (0%RH-20%RH) | ||
Applicable Material Particle Size | (0.2um-10mm) | (0.2um-10mm) | ||
Vertical Conveying Distance | (0m-20m) | (0m-20m) | ||
Horizontal Conveying Distance | (0m-80m) | (0m-80m) | ||
If larger capacity equipment is needed, please contact us for customization. |
How to Select A Vacuum Conveyor>>>
Material Characteristics:
Type of Material: Consider the nature of the material you need to transport. Vacuum conveyors are suitable for powders, granules, capsules, tablets, small components, and other materials. Ensure that the conveyor is designed to handle the characteristics of your specific material.
Abrasive or Fragile: If the material is abrasive, the conveyor should have components designed to withstand wear. For fragile materials, choose a conveyor system that provides gentle handling to prevent damage.
System Capacity and Throughput:
Required Throughput: Determine the desired material transfer rate or throughput. The conveyor system should be capable of handling the volume of material needed for your production process.
Conveyor Size: Consider the physical size of the conveyor system, ensuring it fits within your production space while accommodating the desired capacity.
System Configuration:
Configuration Options: Vacuum conveyors come in various configurations, including single or multiple conveyor lines, flexible tubing, and conveyor belts. Choose a configuration that aligns with your material handling needs and the layout of your production facility.
Customization: Evaluate whether the conveyor system can be customized to meet specific requirements, such as integration with existing equipment, adaptability to different material sizes, or the ability to handle multiple materials.
Cleanliness and Contamination Control:
Hygiene Requirements: In industries like food and pharmaceuticals, cleanliness is crucial. Select a vacuum conveyor with smooth, easy-to-clean surfaces and features that prevent contamination, such as dust extraction systems.
Material Contact Surfaces: Choose a conveyor with material contact surfaces made from materials compatible with your industry standards and regulations.
Ease of Maintenance:
Access for Maintenance: Consider the ease of access for maintenance and cleaning. A conveyor with quick and convenient access points will reduce downtime and ensure efficient operation.
Wear Parts: Evaluate the availability and cost of replacement parts, especially wear parts, to estimate ongoing maintenance expenses.
Power Requirements and Efficiency:
Power Consumption: Assess the power requirements of the vacuum conveyor and its energy efficiency. Choose a system that aligns with your facility's power capabilities and energy conservation goals.
Control Options: Consider the available control options, such as variable speed controls, to optimize the conveyor's performance based on specific material handling needs.
Environmental and Safety Considerations:
Safety Features: Ensure that the vacuum conveyor has safety features, such as emergency stop buttons, guards, and sensors, to enhance workplace safety.
Environmental Impact: Consider the environmental impact of the conveyor system, such as noise levels and any emissions. Choose a system that aligns with environmental regulations and workplace safety standards.
Cost and Return on Investment (ROI):
Initial Cost: Evaluate the initial cost of the vacuum conveyor system and compare it with your budget constraints.
ROI Considerations: Consider the long-term return on investment, factoring in factors such as reduced labor costs, increased efficiency, and potential energy savings.
Supplier Reputation and Support:
Supplier Track Record: Choose a reputable supplier with a proven track record in providing reliable vacuum conveyor systems.
Customer Support: Assess the level of customer support provided by the supplier, including availability of technical assistance, spare parts, and maintenance services.
Packing And Delivery>>>
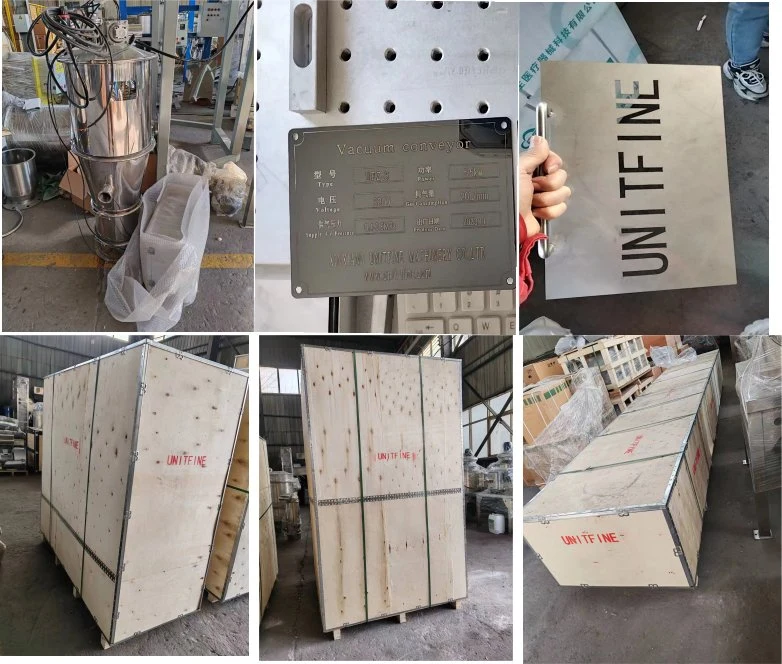
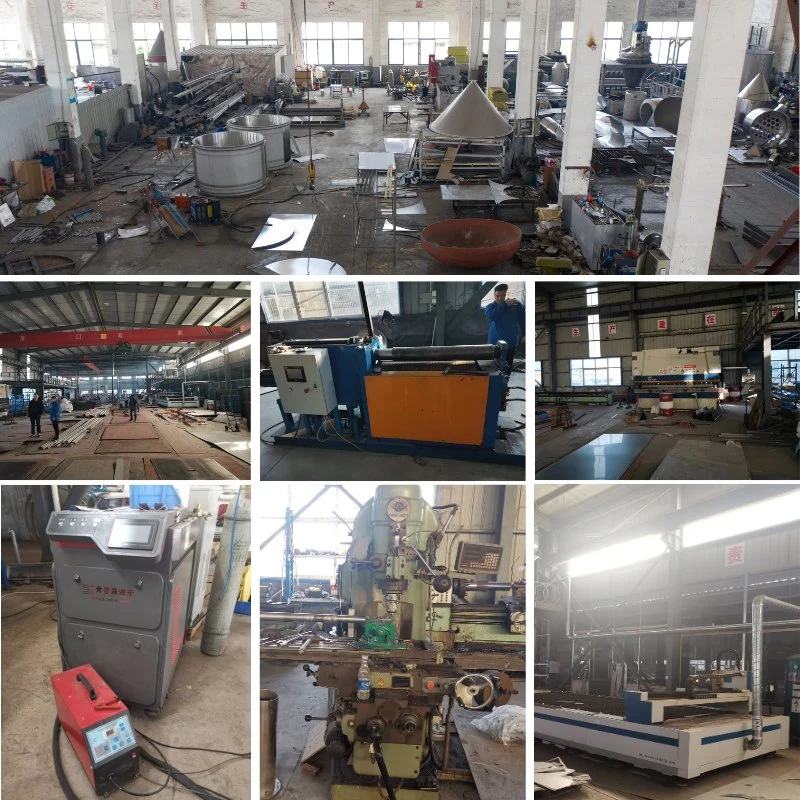