- Overview
- Product Description
- Work Principle
- Features
- Product Parameters
- Customer site
- Company Profile
- Packaging & Shipping
- Our Service
Basic Info.
Packaging & Delivery
Product Description
High Pressure Roller Mill also known as high pressure Raymond Mill, referred to as high pressure grinder, high pressure mill, high pressure roller mill, high pressure roller grinder.
Reymond Mill of our company is a strengthened type, combining the successful experience at home and abroad and popular Raymond Mill technology optimization upgrade. The biggest improvement is the addition of a high-pressure spring system for the roller section. With a wider range of grinding materials, grinding particles finer, grinding efficiency higher outstanding advantages, is a highly efficient energy-saving mill equipment.
Widely used in mining, construction, building materials, Water Conservancy, hydropower, metallurgy, chemical and other industries in the material processing field, such as calcium carbonate grinding, gypsum powder processing, power plant desulphurization, non-metallic mineral powder, coal powder preparation and other industrial grinding projects.
[Input Size]<35mm [Output Size] 0.33-0.19mm [Product Capacity]0.4-35t/h
YGM1500 YGM130
High-pressure hanging roller mill host, roller hanger fastened with 1000-1500 kg pressure of high-pressure spring. After starting work, the roller rotates around the main shaft, and under the action of high-pressure spring and centrifugal force, it rolls close to the grinding ring, and its rolling pressure is 1.2 times higher than that of Raymond Mill under the same dynamic condition, as a result, the output was greatly increased. When the ground material enters the grinding chamber, it is picked up by the shovel and sent to be rolled between the grinding roller and the grinding ring. The rolled powder is brought into the analyzer with the circulating air of the blower. The qualified fine powder flows into the cyclone collector with the air and is the finished product, large particles fall back to regrinding. The circulating air returns to the blower to repeat the above process, and the residual air enters the bag filter for purification. When the roller and ring reach a certain degree of wear, adjust the length of high-pressure spring, keep the constant roller and ring between the grinding pressure, so as to ensure a stable output and fineness.
The whole equipment of high-pressure hanging roller mill consists of main machine, reducer, analyzer, pipeline device, fan, dust collector, jaw crusher, bucket elevator, electromagnetic vibration feeder, electric control system, etc. .
Features
1. YGM1500 mill analyzer adopts cage-type separator, which is easy to adjust, the fineness of powder is more fine, and the output is significantly increased.
2. Air duct and Shell adopt arc design, reduce air resistance and increase output.
3. Compared with the common Raymond Mill, the output is increased by 10% -30% under the same dynamic condition, and the roller's rolling pressure on the material is increased by 1500kgf under the action of high pressure spring.
4. The finished product has a wide range of particle size, with the largest particle size up to 0.95 mm (20 mesh) , the fine powder particle size up to 600 mesh, and a few materials up to 0.013 mm (1000 mesh) .
5. The fineness uniformity of the finished products can reach 98% of the required particle size, that is, 98% through the sieve. This is the other grinding equipment can not be competent.
6. The main engine adopts the closed gear box, the transmission is stable and the operation is reliable. The important parts of the mill are made of high-quality steel, so the whole machine is durable and reliable.
7. The electric system adopts centralized control, advanced and reasonable selection, high degree of automation, small volume and light weight of vibrating feeder, even feeding, easy to adjust and save electricity, easy to use and maintain.
8. The grinding device adopts overlapping multi-stage seal, which has good sealing performance and dust removal effect fully meets the national dust emission standard. 9. The whole machine is a vertical structure, which is characterized by a small area, complete set of strong, from block material to powder to finished powder, packaging, can be an independent production system.YGM1500 type pulverizer is quipped with cage analyzer,new type reducer and variable frequency speed control feeding belt conveyor,which has high transmission effiency.stable operation and convienient maintenance.
Model | Grinding roller number | Max.feeding size(mm) | The final size(mm) | Capacity(t) | Powder(kw) | Overall dimension(m) |
YGM65 | 3 | 15 | 0.613-0.033 | 0.4-1.8 | 15 | 4.1x3.3x4.5 |
YGM75 | 3 | 15 | 0.613-0.033 | 1-3 | 18.5 | 4.3x3.5x5.1 |
YGM85 | 3 | 20 | 0.613-0.033 | 1.2-4.6 | 22 | 5.3x4.1x5.2 |
YGM95 | 4 | 25 | 0.613-0.033 | 2.1-5.6 | 37 | 7.1x5.9x7.9 |
YGM130 | 5 | 30 | 0.613-0.033 | 3-9.5 | 75 | 7.85x8x9.7 |
YGM1500 | 4 | 30 | 0.95-0.038 | 5-10 | 90 | 11.15x7.48x10.23 |
YGM160 | 6 | 35 | 1.9-0.045 | 8-16 | 132 | 12.55x7.5x8.355 |
YGM190 | 5 | 35 | 0.613-0.033 | 12-26 | 200 | 11.47x6.94x9.58 |
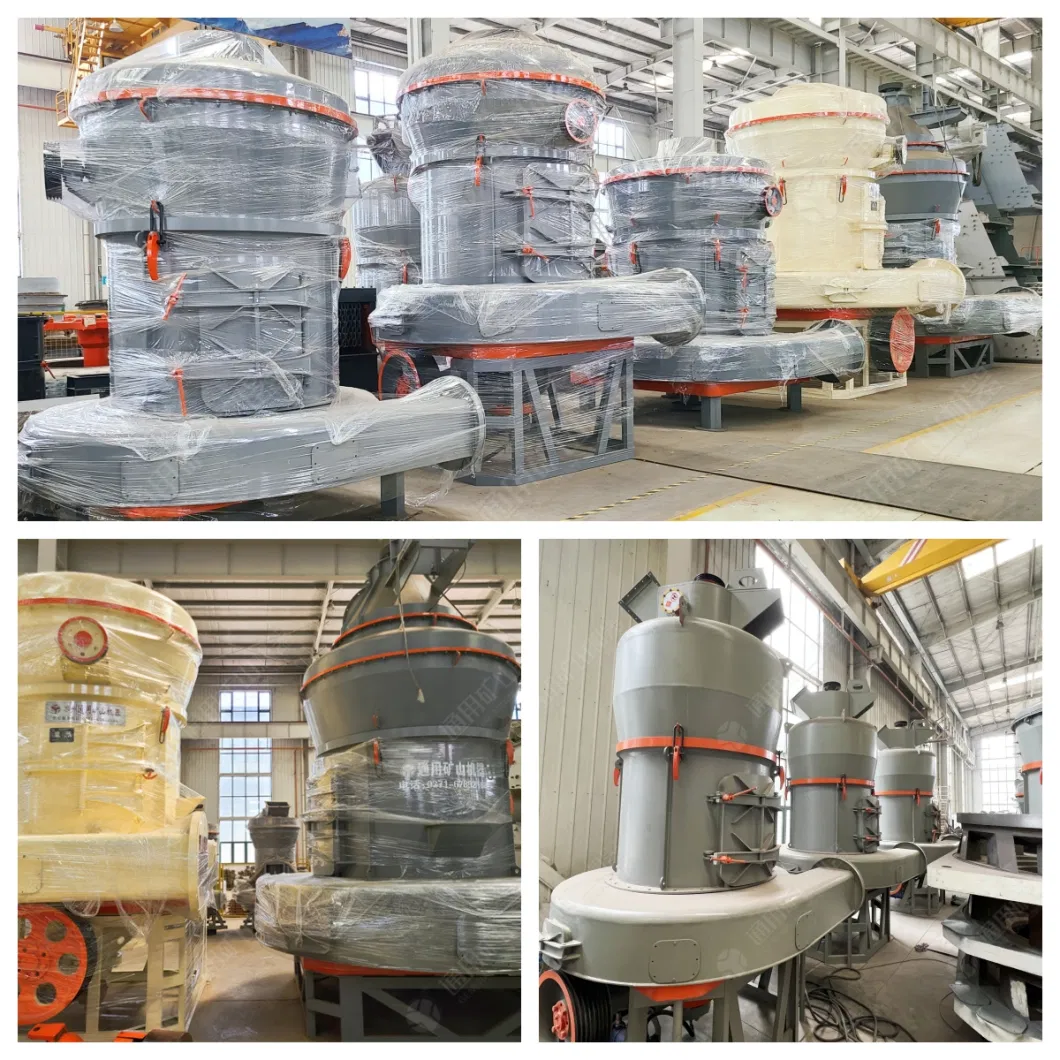
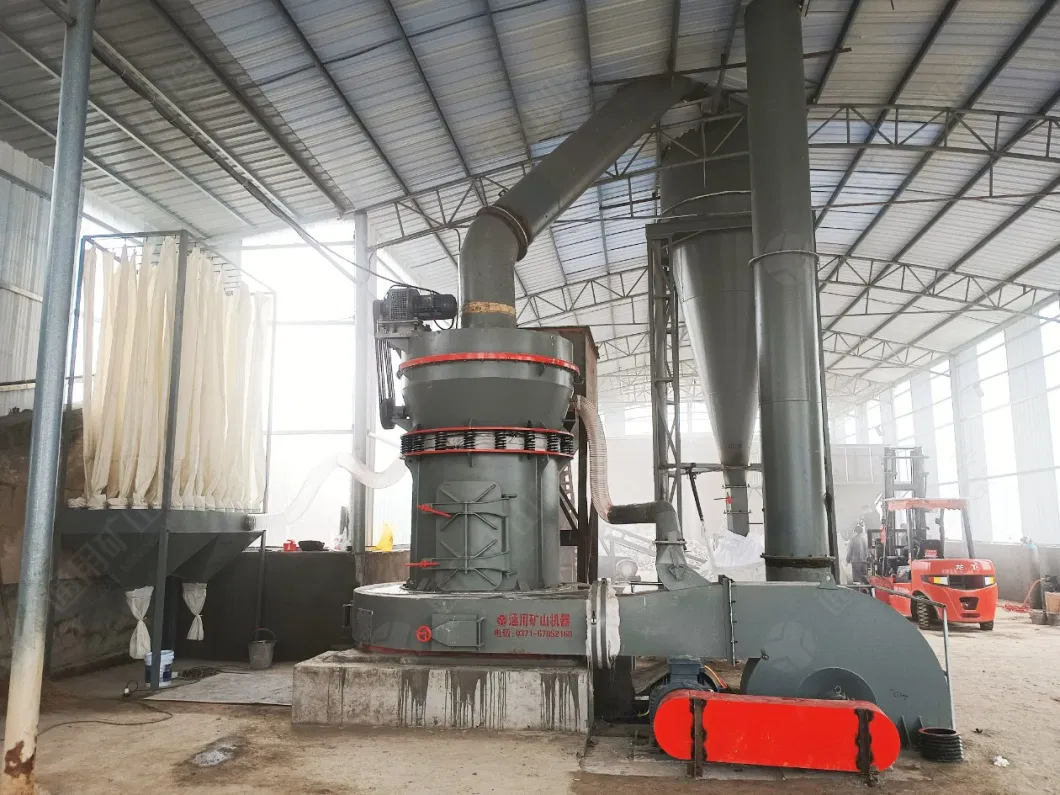
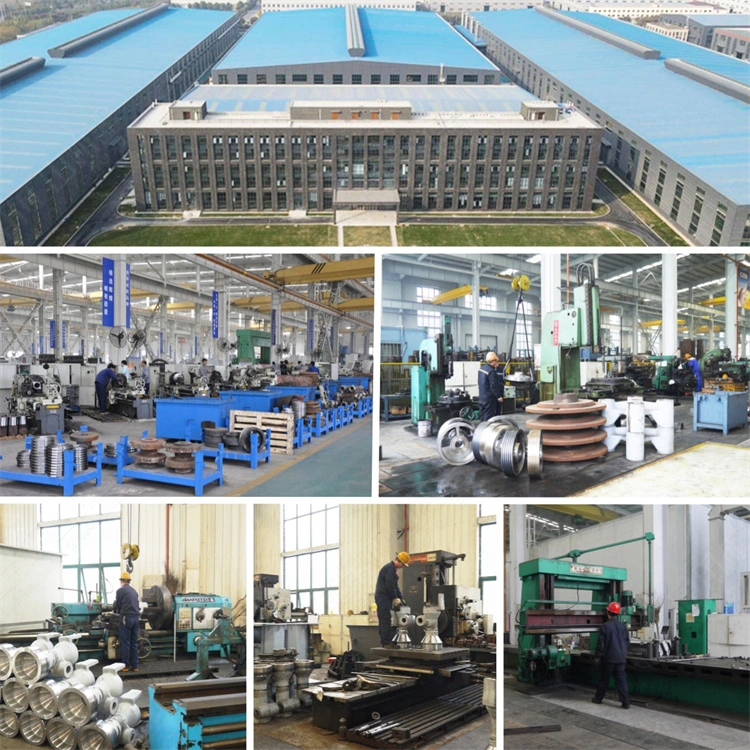
The package of all equipment is accord with the standard protective measures.The packing is suitable for short and long distance transportation. The moisture proof, quake proof, protected against dampness, and rustproof protection measures were taken to ensure the machine shipping to customers safely. All the machine will be packaged by plastic film.
Warranty 100% brand new when leaving the factory. The seller guarantee quality of the machines (excluding wearing parts) for a period of one year from the date of trial run finish under our technician's guidance, but not exceed 15 months from date on which machine leaves the factory.
Pre-sale services:
(1) Device model choice.
(2) According to customer's special requirements, design and manufacture of products.
(3) Training technical personnel for clients.
(4) The company is free of charge to the user on-site engineering and technical personnel planning site for the user to design the best processes and program.
Sale services:
We will send technicians to you for guiding the equipment installation and commissioning and staff training.
Sales tracking :
(1) product acceptance.
(2) to help customers develop construction programs.
After-sale services :
(1) Guiding customers' installation.
(2) On-site training of operators.
(3) Complete sets of equipment installed, 1-2 full-time technical staff to stay free of charge to help customers on-site production of 1 month, until the user' satisfaction.
Contact us to get more details,answer the follewing questions to recommend the right machine for you.
1.What's the raw materials?
2.What is input size of raw materials?
3.What size of discharge do you want?
4.What product capacity do you need?
5.Please tell me your wahtsapp number so that we can talk more details